Oklahoma Steel Buildings are a popular choice for commercial spaces because they can be erected quickly and cater to wide open floor plans. They also offer a high level of durability.
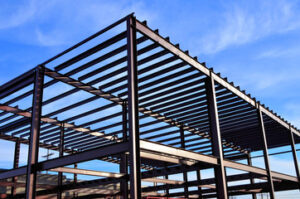
The construction process of a steel building begins with site preparation. This includes removing any obstacles and properly leveling the ground.
When you’re constructing a steel building, much of the work is done offsite. Plans are engineered, and the building kits are pieced together in a warehouse and then delivered to your site for installation. However, the success of your build depends on how well you prepare the site before construction begins.
When looking for a location on your property to put your new metal building, there are four key factors to consider: drainage, orientation, accessibility, and paving. Drainage must be ensured to prevent soil erosion, which could weaken the foundation of your building. You’ll also want to make sure your building won’t interfere with any existing utilities like gas, electricity, and water lines. Finally, you’ll need to know where on your property will require permanent paving so you can accommodate that in your project plans.
The first step in proper site preparation is to clear all obstacles from the area where your steel building will be placed. This includes removing all vegetation, stumps, and large rocks. Then, the ground must be leveled and compacted in order to support the structure and facilitate construction processes like laying the foundation. Depending on your soil conditions, you may need to add fill dirt to create a stable foundation that won’t shift over time.
Once you’ve cleared the area and prepared the foundation, it’s time to start construction on your steel building. During this phase, a professional will lay the foundation based on your preferred method. Then, they’ll begin assembling and erecting the walls and roof components based on your blueprints. With careful planning, possibly under the guidance of a project manager, you’ll be able to construct your steel building with ease.
When selecting a location for your new steel building, it’s important to take into account your building use and future expansion options. Choose a design that allows you to adjust the layout for future expansions without adding cost or compromising safety standards. Additionally, make sure you adhere to all local zoning laws and check if you need any permits before starting your project. By following these tips, you’ll ensure that your project goes off without a hitch and your building is constructed according to engineering specifications.
Foundation
Steel buildings need a strong foundation to transfer the weight of the building to the ground and prevent the structure from shifting or collapsing. A quality foundation requires careful planning and execution, starting with a thorough assessment of the site. This includes removing any obstacles that could hinder construction, leveling the ground surface, and compacting the soil to prevent settling over time.
Once the site is prepared, a concrete foundation can be poured. A concrete contractor must take several factors into consideration, including the amount of concrete needed, curing and protection requirements, and the environmental conditions of the site. For instance, cold weather may cause the concrete to crack as it cures. To prevent this, chemical accelerators can be added to the concrete mix to speed up the process.
The type of soil on which the steel building will be built also plays a significant role in foundation selection. A professional will test the soil to determine its load-bearing capacity, moisture content, and potential for shifting. This information will help the contractor select the appropriate foundation system for the project.
A concrete slab-on-grade foundation is ideal for most metal building applications, but other types of foundations are available for specific situations. For example, foundations designed for areas prone to high winds require special reinforcement to protect the steel structure against uplift and lateral forces. In addition, pile foundations are suitable for soils with low bearing capacity or in situations where the structure must be located close to the water’s edge.
When choosing a foundation, it’s important to consider future expansions and modifications. A flexible foundation can accommodate these needs and save you money down the road.
Another factor to consider is the longevity of the concrete slab. Choosing galvanized or zinc-coated steel for the concrete is an economical way to extend its lifespan and prevent corrosion over time. In addition, galvanizing and zinc-coating protects the steel from oxygen and salt that can erode it.
Design
When it comes to steel building design, there are a few key points that must be taken into consideration. First, decide what you’ll be using the structure for. This will help determine the layout and size you need for your equipment, tools, or office space. It will also make it easier to choose options like insulated panels, which are beneficial for reducing energy consumption and costs.
Depending on your use, you may need to include large, open spaces or plenty of room for parking cars and trucks. You’ll also need to consider whether you’ll be constructing a workshop, garage, or an office, each of which has different needs that require a unique design. Once you’ve figured out what your steel building will be used for, it’s time to create a blueprint of your project. A well-designed plan can save you money, frustration, and time in the long run.
A steel structure’s foundation is essential for its durability and longevity. Excavating the area, setting up formwork, and pouring and curing the concrete are all important steps in ensuring a sturdy, durable foundation that will support the building. If any of these steps are not done correctly, your steel building could eventually collapse or suffer other damage.
The location of your steel building is another important factor in its design. Be sure to avoid placing it near any other structures or land features that might interfere with your work space or impede traffic flow. If possible, try to place your building in an area that will allow for easy future expansions as your business grows.
When choosing a general contractor to build your steel building, be sure to research their skills and experience. You’ll want to find someone who has worked with metal buildings before and knows how to handle the materials and assemble them efficiently.
Finally, it’s important to make sure your steel building is properly insulated. This will help reduce your energy costs, prevent condensation, and make it soundproof. There are several different types of insulation available, so choose the one that best suits your needs and climatic conditions.
Assembly
Steel buildings provide an attractive, functional storage solution for many different applications. They offer durability and strength, while saving time on construction and cost. However, there are several considerations to keep in mind when using this building type. For example, it is important to follow proper installation procedures to ensure safety and performance. Moreover, it is crucial to use the correct materials and components. This will help to ensure the longevity of the building.
The assembly of a steel building requires precise planning and attention to detail. The process begins with excavating the site and laying foundations. The concrete is then poured and leveled. Finally, reinforcement bars are placed to prevent cracking and provide strength. This entire process is crucial for the longevity of your steel building.
When it comes to constructing a steel building, you need a team of professionals with experience in the field. The process is streamlined, and the building is ready for use within a shorter time than other types of buildings. The cost is also much lower than other building types, making it a more affordable option for businesses.
In addition to the cost savings, steel buildings can be erected quickly and are highly customizable. This makes them an excellent choice for businesses that require massive warehouse space. Unlike other construction methods, steel structures can accommodate wide floor plans without requiring expensive modifications. Moreover, they are designed with durable, low-maintenance materials that can withstand harsh weather conditions.
While the assembly of steel buildings varies between contractors, the general process is similar. The building is anchored into the ground with anchor bolts. These bolts transfer the load from the columns and rafters to the foundation. These bolts are typically placed before the concrete is poured to avoid costly mistakes.
Before starting the erection of a steel building, it is crucial to review the building drawings and instructions. This will help you understand the process better and ensure that all parts are installed correctly. It is also important to follow safety guidelines and seek assistance when necessary. This will protect you and your employees from injuries and other safety hazards.