With 3D printing, product designers can create prototypes more quickly, test designs with consumers faster, and bring new products to market much sooner.
In addition, manufacturing is more accessible to companies and individuals. They can create products without investing in large factory facilities or shipping them long distances. Visit our Website to learn more.
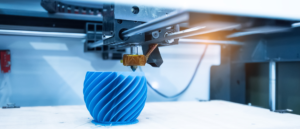
3D printing turns a digital 3-dimensional CAD model into a physical solid object by adding material layer by layer. It’s the opposite of subtractive manufacturing, which works by carving away materials to create a part. 3D printers allow complex shapes to be made that would otherwise be difficult or impossible with traditional methods, which is why they’re transforming the manufacturing world.
The technology’s popularity has reached a level where it’s being referred to as a “next-generation industrial revolution.” Some experts believe it could even be bigger than the Internet. As such, it’s important to understand exactly what this type of manufacturing entails.
While it’s often compared to other manufacturing processes, like casting and forming, the primary distinction of 3D printing is that it is additive, rather than subtractive. The technology builds up a solid object by depositing material in layers, so the term is used to refer to all types of additive manufacturing.
It can take minutes to over an hour for a printer to build a single layer. Then, it moves on to the next. The print time depends on the size of the printed object, its printer type and the material used. A few hours is typical for plastics, while metals and concrete can be produced in a matter of minutes.
The strength of the final object also depends on its material. Typically, plastics are the strongest, while metals and concrete are the most durable. However, there are also specialized materials like water-absorbing plastic, nitinol and gold. These offer unique properties like heightened heat resistance and water repellency, making them an ideal choice for certain applications.
Many companies use this technology to prototype new parts or components before putting them into full-scale production. The Protolabs Network is a good example, creating high-quality, durable plastic housings for electronic devices that boast resistances to various elements. These are then paired with injection-molded parts to produce finished products that customers can enjoy.
Another big use case for the technology is supplying spare parts to consumers. This can be done by creating a CAD file of the replacement part and printing it on demand. This saves the company money on shipping, storage and inventory costs. It also gives customers greater access to a more versatile product, because they don’t have to wait for an entire batch of new parts to be manufactured.
How It Works
3D printing is an additive process that builds up a physical object layer by layer. Each printed layer is like a finely sliced cross-section of the final product. This differs from traditional manufacturing processes, which carve away or hollow out objects, and is referred to as additive manufacturing because it adds material rather than subtracting it.
A wide range of materials can be printed in 3D, including metals, plastics, ceramics, and concrete. These materials are used for rapid prototyping, which helps reduce the cost and time of a new product design. However, the potential for 3D printed materials to be used in manufacturing production components is even more exciting.
As the cost and complexity of 3D printers have dropped, they’ve become an indispensable tool for engineering, product development, medical applications, and many other industries. The technology can be used to quickly create and test prototypes that look and function much like the final products, allowing engineers to identify and fix design flaws before moving to full production. For example, when the company behind Plaato developed its optically clear airlock for homebrewing, they printed 1,000 prototypes to test and refine their product before committing to costly tooling.
In addition to speeding up the product development cycle, 3D printing can also improve assembly times by reducing the number of parts needed for an assembly and allowing designers to consolidate complex geometries into more manageable units. This can help to cut down on assembly time and improve quality by reducing the risk of weak joints, overhangs, or other problems that can arise during assembly.
There are upwards of a dozen different 3D printing technologies and processes in use today, from the first stereolithography (SLA) machines to desktop-friendly fused deposition modeling (FDM) printers to selective laser sintering (SLS) and direct metal fabrication (DMF). Depending on the print method, the printer may work by curing liquid resin using UV light, by melting or fusing small particles of polymer powder at high temperatures, or by depositing and fusing strands of solid material. Most modern systems can run unattended until the print is complete and automatically replenish the printer with new material from cartridges. Once the prints are finished, they require rinsing in isopropyl alcohol to remove any uncured resin and post-curing to stabilize their mechanical properties.
Materials
The most common materials used in 3D printing are thermoplastic and thermoset polymers, but metals, ceramics and other materials can also be printed. The most popular plastic filaments are PLA (polylactic acid), ABS (acrylonitrile butadiene styrene), and PP (polypropylene). PLA is one of the most versatile printing filaments, as it’s biodegradable and can be made from renewable sources like corn starch or sugar cane. It’s also relatively inexpensive, compared to other filament types.
Other 3D printing materials include polycarbonate, which is highly heat-resistant and often added to other filaments for additional strength; PETG, or polyethylene terephthalate glycol, which offers durability, chemical resistance, and transparency; and glass-filled nylon, which adds strength and flexibility to the finished print. Carbon fiber, which is woven into composites that are layered with other filament materials, can also be used to strengthen plastic objects and provide electrical conductivity.
For those looking to print items with a more traditional appearance, wood filaments are available that use finely ground wood powder mixed with polymer glue. These printed items are able to look like a lighter or darker version of real wood depending on the printer’s temperature settings. Another option is a metal filament, which prints objects with the look of a variety of different metals, including steel, bronze, brass and copper. Metal is also a popular choice for industrial applications as it’s strong, durable and resistant to corrosion.
Stainless steel is an extremely popular choice for metal 3D printing, as it’s a great material for household fixtures and appliances that are designed to withstand corrosion. In addition, it’s a popular choice for medical and aerospace applications where there’s a need for lightweight parts that can be assembled quickly. Another growing trend in the industry is using a process called direct metal laser sintering to 3D print parts from metal. This allows for a much faster manufacturing process than traditional fabrication methods and helps to reduce costs. It’s also a good alternative to using traditional casting techniques for end-use metal products, as it can produce items with more complex shapes and features that are typically difficult or impossible to make by hand.
Software
There are a number of software programs that can be used to design, prepare, and manage 3D printing processes. These include CAD software, slicers, and 3D printer host programs. CAD software is used to create the initial digital model of the object that will be printed. This is a powerful tool that can be used to create complex shapes and structures with precision. Depending on the application, CAD software can be used to make adjustments to the model, including modifying dimensions, adding materials or support, and creating a layered file that is compatible with a specific 3D printer.
The next type of software is a slicer, which is used to prepare the digital model for printing. This process is essential for converting the CAD model into a printable format that a 3D printer can understand. Slicing software can be used to remove unnecessary parts, scale a model, and make other modifications to optimize the print for particular materials or printer capabilities. It can also be used to generate a series of commands for the printer that will guide it through the print process.
Finally, 3D printer hosting software allows users to monitor and control their 3D printers remotely. This can be helpful for businesses that need to outsource their printing needs, as it can save time and money by eliminating the need for in-person printer management. 3D printer host programs can be used to start and pause print jobs, adjust the print settings, and even receive notifications about any errors or completion of prints.
A popular choice is Autodesk Fusion 360, which is a powerful and flexible tool for designing 3D models and preparing them for 3D printing. It features a variety of tools for modeling, sculpting, rendering, and animation, making it a great option for professional designers. Another popular choice is Rhino3D, which offers a suite of surface modeling and parametric modeling tools for a wide range of applications.
Lastly, there is IceSL WebPrinter, which allows users to load G-code files directly through a web interface, allowing them to easily monitor and modify their prints from anywhere. This is a convenient option for users who need to access their printers from a remote location, and it can be used on any device with an internet connection.